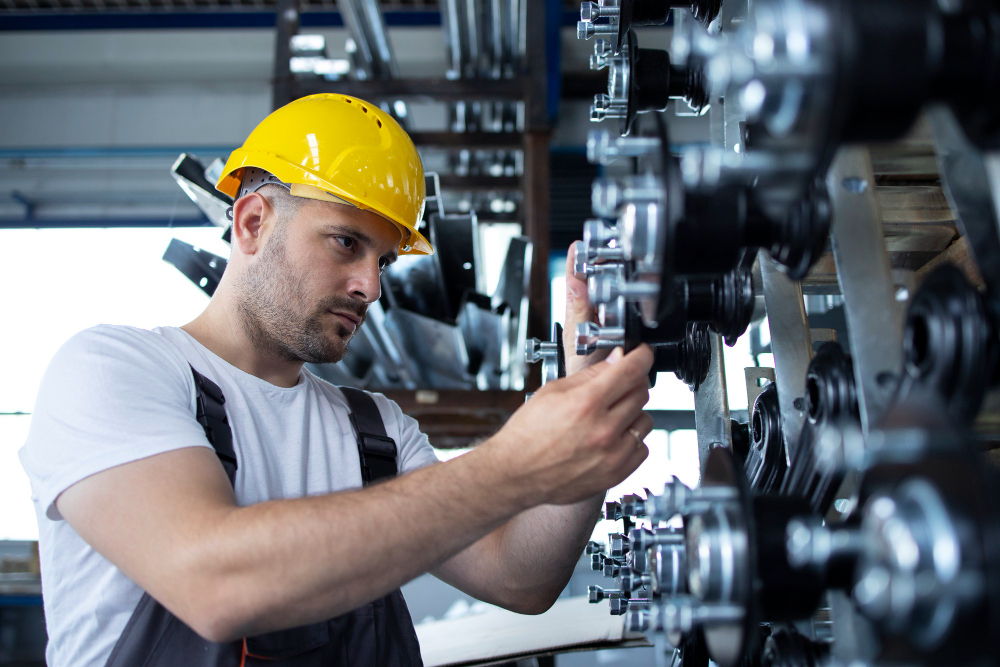
Brak właściwej diagnostyki silników elektrycznych może przynieść wiele strat, m.in. znacząco obniżyć sprawność maszyny, zwiększyć zużycie energii, powodować nieplanowane przerwy w pracy. Badanie w zakładzie przemysłowym jest więc rozwiązaniem nie tylko koniecznym, ale i ekonomicznym. Taka analiza zapobiega niepotrzebnym przeglądom i remontom, bowiem konkretnie określa problem i decyduje o losach napędów.
Celem diagnostyki silnika elektrycznego jest ocena bieżącego stanu technicznego, wyszczególnienie przyczyn zaistnienia danego problemu oraz określenie czasu potrzebnego do zmiany kondycji maszyny. Obiektywną ocenę stanu urządzenia umożliwiają pomiary parametrów, do których należą m.in. moc, prędkość, prąd, luzy, odchyłki kształtu i wymiarów w stosunku do wzorca, drgania, hałas, strumień osiowy.
Najczęściej spotykanymi problemami maszyn są uszkodzenia mechaniczne łożysk oraz izolacji uzwojeń silnika. Są one kosztowne w naprawie, dlatego też zdecydowanie warto poddawać maszyny w przemyśle regularnej diagnostyce. Innymi przyczynami awarii są również uszkodzenie obwodu elektrycznego i mechanicznego oraz problemy ze szczeliną pomiędzy stojanem a wirnikiem. Ważną kwestią, jeśli chodzi o problemy z izolacją, jest niekierowanie zbyt szybko silnika na przezwojenie, bowiem jej stan często umożliwia jeszcze pracę przez dłuższy czas (przewidziany przez diagnostyka). Należy jednak pamiętać, że jeśli izolacja jest w naprawdę kiepskim stanie, nie powinno się dopuszczać do eksploatacji silnika. Tu po raz kolejny pojawia się korzyść z monitorowania stanu elektrycznych urządzeń – m.in. procesu starzenia się wspominanej izolacji.